Students Customize Electric Guitars, Inspired by Investment from Rock Band
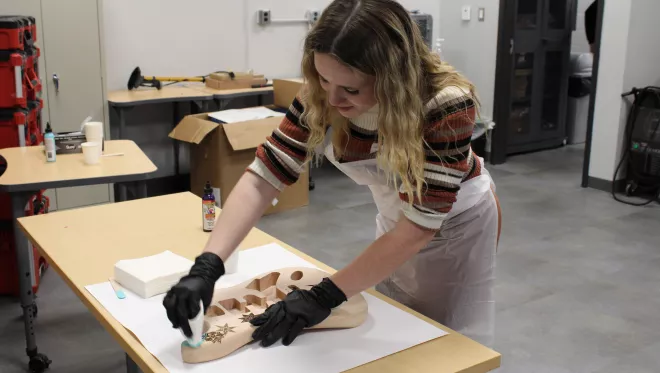
Published
Field of Study
Engineering TechnologyTCC Engineering Technology students are designing and assembling custom electric guitars in the College’s Fab Lab, combining creativity with technical skills. Inspired by the Metallica Scholars Initiative, the project encourages hands-on learning and innovation.
Students in Tulsa Community College’s Engineering Technology program are blending creativity with technical skills by designing, customizing and assembling electric guitars inspired by the Metallica Scholars Initiative (MSI).
MSI, launched by Metallica’s non-profit foundation All Within My Hands, provides funds for career and technical education programs at community colleges across the U.S.
TCC is one of 18 colleges selected for MSI’s sixth cohort and the only recipient in Oklahoma. The $75,000 grant is dedicated entirely to student scholarships. To date, more than $29,000 has been awarded to 44 students majoring in Air Traffic Control, Commercial Pilot, Engineering or Engineering Technology.
Learning by Doing
In TCC’s Fab Lab, TCC Assistant Professor Caleb Crall encourages his students to apply what they learn in class to personalize and craft their own instruments.
Students are using design software to customize the body of wooden guitars, paid for by TCC. They bring their designs to life using the Fab Lab’s full-size laser engraver machine. After engraving, they seal the wood before learning to assemble and attach the guitar’s electronics.

Student and Metallica Scholar Jennifer Slimp took inspiration from her granddaughter for her custom guitar design, incorporating etched images of her into the instrument’s body.
“I wanted the design to have a musical theme, almost like a bedtime story,” Slimp explains. “I chose some of my favorite pictures of my granddaughter, added musical notes and learned to use the wood engraving machine to imprint them onto the guitar.”
After completing her design, Slimp stained the guitar body, applied a protective coat and then installed the guitar’s electronics.
“When I plugged it into an amp, it needed some tuning, but it worked,” she recalls proudly.
Slimp says she first attended TCC years ago and returned to finish her degree in Manufacturing Engineering.
“I only have few classes left, so I came back to finish my to further my career as a quality engineer,” says Slimp. “I didn't think I could ever do some of the things we’ve been doing in the Fab Lab, so I’m really happy to have the opportunity to be here and learn.”
Slimp says she will gift her guitar to her granddaughter as a keepsake.
Innovation in the Classroom
Now in his second year at TCC, Crall says he was motivated by the investment from legendary rock band Metallica to incorporate elements of the music industry into his course curriculum.
“When we got this opportunity with the Metallica Scholars Initiative, I wanted to show that we can utilize our manufacturing facilities to make something unique,” says Crall. “First, the students learned the design software and we started with designing a guitar pick. Then we started designing our guitars.”
Crall describes the process as a learning experience for everyone, including himself.
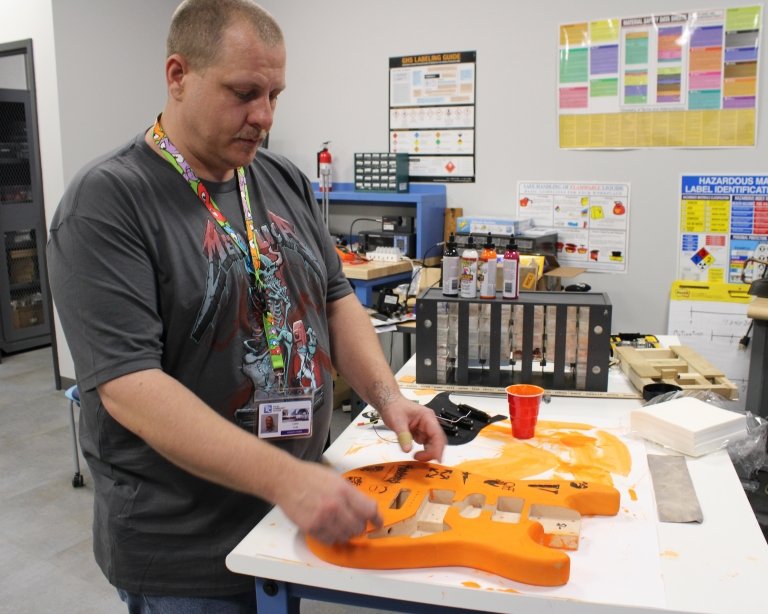
“I’ve played guitars before, but building one was a first for me too,” Crall shares. “This was a learning experience for all of us. It’s about showing students that creating something like this is achievable. It’s about embracing the engineering design process.”
Crall tries to challenge his engineering students to think outside the box to develop a problem-solving mindset.
“I'm big on the engineering design process where we design it, build it, redesign it, rebuild it and we keep going. I think a lot of students struggle with the thought of needing to go back to that drawing board, but that’s part of the process to making something better.”